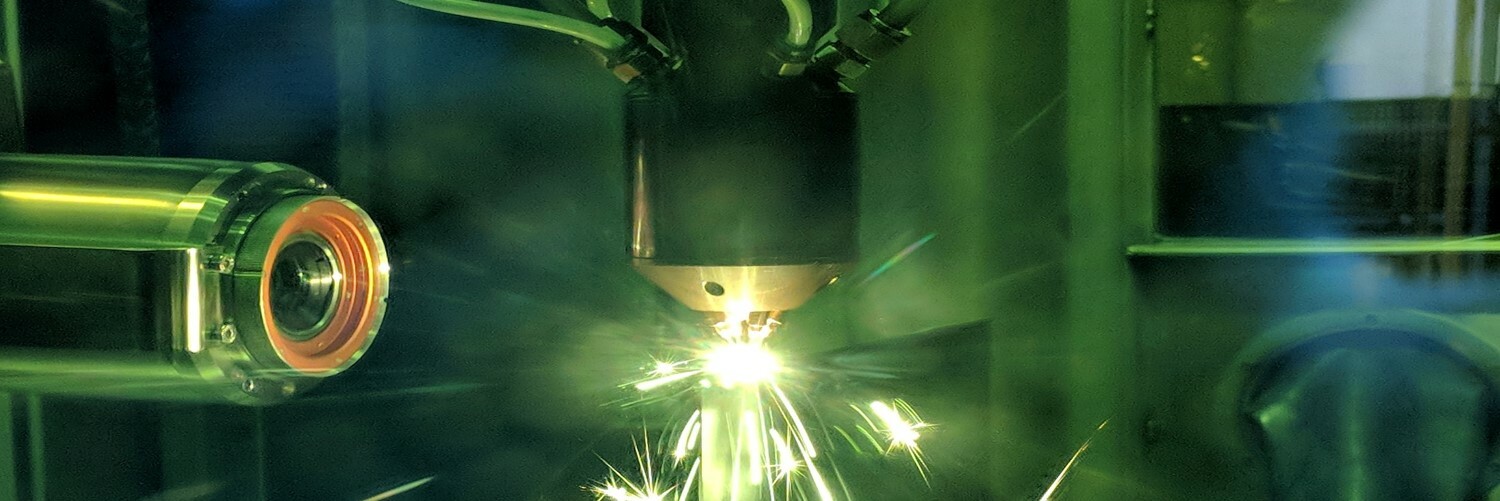
In 2014 as part of a robust New York State economic development initiative called the Buffalo Billion, EWI was selected to establish an advanced manufacturing center in Buffalo, N.Y. After thoughtful planning, Buffalo Manufacturing Works, operated by EWI, opened in April 2015 on the Buffalo Niagara Medical Campus. The team immediately got to work helping innovation-driven organizations excel by partnering with their internal manufacturing, engineering, and R&D teams to deliver better products, grow, and compete.
After just a few years, it became clear that a new, larger facility would be needed as the team grew and additional state-of-the-art equipment was purchased to support the mission.
In 2018, Buffalo Manufacturing Works made the move to the Northland campus in East Buffalo, doubling its square footage and joining the Northland Workforce Training Center in anchoring the transformational Northland Beltline corridor.